UTB a PFNonwovens aim together at circular waste management for nonwovens textiles production
Researchers from the Tomas Bata University Polymer Systems Center in Zlín are taking another step towards waste-free management together with PFNonwovens, a leading global manufacturer of nonwovens based in the Czech Republic. The research and development project “Technological production scrap as an innovative material source in a process of production of nonwoven textile” (FW03010465) of the TREND program is underway from 2021 to 2024 with the support of the Technology Agency of the Czech Republic (TAČR).
Nowadays, it is increasingly challenging to make production even more sustainable. Low hanging fruits have already achieved, leaving the more complex issues to be resolved. Nonwovens are a perfect example. Spunmelt nonwoven fabrics are widely used in disposable absorbent hygiene products (e.g. diapers), disposable protection and sanitary items used, for example, in hospitals or doctors’ offices. Today, everyone uses some type of these products (face masks / respirators also comprise spunmelt nonwovens); what’s more: we all require both perfect functionality and comfort. To reach the goal in each chosen application, each nonwoven filament with a thickness of less than quarter of a human hair is comprised of more polymer components exactly distributed along the entire length of the fibre. Any scrap from this production process presents a real challenge for recycling. "We need to consider that such waste, especially in the molten state during further processing, presents a dispersed mixture of immiscible polymers. We can imagine it as a salad dressing containing both water and oil, where bubbles of each liquid are really small, in fact so tiny, that you cannot effectively divide them for separate use. On the contrary, these bubbles are big enough to prevent simple recycling, as they break the filaments during formation," explains doc. Tomáš Sedláček, Head of the Polymer Processing Research Division at the Centre for Polymer Systems (CPS).
The CPS operates a laboratory spunmelt line that is suitable to be used as a model for large commercial lines able to produce several tons of nonwoven material in one hour. "The cooperative relationship between PFN and CPS allows us to understand the position and problems of the spunmelt producer and helps us to prepare our students better for real applications in the industry. PFN uses our laboratory line as the first stage for testing new polymer/additive blends and filament compositions. The current project allowed us to deepen our cooperation, study and describe the issues in greater detail and search together for solutions in this challenging task. The synergy of production-focused developers and our academic researchers is a win-win situation for everyone involved," says doc. Tomáš Sedláček.
The first year of the project was focused on studying polymer blends from the regranulation process, which provides polymer pellets from nonwoven scrap material. Research work at the CPS was combined with trials conducted on PFN's commercial lines and semi-commercial pilot lines to find critical features in the process and link them to laboratory results. "Data collected this year already brought some unexpected surprises," doc. Tomáš Sedláček admits. "Our task is to find a way how to amend polymer composition during regranulation to create raw material for spunmelt production. I personally see a big potential in this field; our findings might be applicable in the future, especially with respect to polymer mixtures from various sources. Last but not least, I personally appreciate the approach PFN is taking in the field and their focus on sustainability."
Simon Frisk, Global Head of RD at PFN adds: “This project is another great example of the power of collaboration between industry and academia, and between PFN and UTB in particular. Together, we study and develop solutions to complex fundamental polymer issues or developments. The deep polymer knowledge and expertise of UTB, together with their advanced laboratory capabilities, constitute an ideal partner for PFN to tackle some of our more complex challenges. The solutions developed in the laboratories are then rapidly applied to our commercial operations, providing students with direct examples of how laboratory work can have a big impact in the industry. For this particular project, the impact goes beyond good science and technology development. It will enable the reduction of the environmental footprint of our products by reducing waste and reusing raw materials, contributing to PFN’s overall drive to be an industry leader in sustainability.”
Nowadays, it is increasingly challenging to make production even more sustainable. Low hanging fruits have already achieved, leaving the more complex issues to be resolved. Nonwovens are a perfect example. Spunmelt nonwoven fabrics are widely used in disposable absorbent hygiene products (e.g. diapers), disposable protection and sanitary items used, for example, in hospitals or doctors’ offices. Today, everyone uses some type of these products (face masks / respirators also comprise spunmelt nonwovens); what’s more: we all require both perfect functionality and comfort. To reach the goal in each chosen application, each nonwoven filament with a thickness of less than quarter of a human hair is comprised of more polymer components exactly distributed along the entire length of the fibre. Any scrap from this production process presents a real challenge for recycling. "We need to consider that such waste, especially in the molten state during further processing, presents a dispersed mixture of immiscible polymers. We can imagine it as a salad dressing containing both water and oil, where bubbles of each liquid are really small, in fact so tiny, that you cannot effectively divide them for separate use. On the contrary, these bubbles are big enough to prevent simple recycling, as they break the filaments during formation," explains doc. Tomáš Sedláček, Head of the Polymer Processing Research Division at the Centre for Polymer Systems (CPS).
The CPS operates a laboratory spunmelt line that is suitable to be used as a model for large commercial lines able to produce several tons of nonwoven material in one hour. "The cooperative relationship between PFN and CPS allows us to understand the position and problems of the spunmelt producer and helps us to prepare our students better for real applications in the industry. PFN uses our laboratory line as the first stage for testing new polymer/additive blends and filament compositions. The current project allowed us to deepen our cooperation, study and describe the issues in greater detail and search together for solutions in this challenging task. The synergy of production-focused developers and our academic researchers is a win-win situation for everyone involved," says doc. Tomáš Sedláček.
The first year of the project was focused on studying polymer blends from the regranulation process, which provides polymer pellets from nonwoven scrap material. Research work at the CPS was combined with trials conducted on PFN's commercial lines and semi-commercial pilot lines to find critical features in the process and link them to laboratory results. "Data collected this year already brought some unexpected surprises," doc. Tomáš Sedláček admits. "Our task is to find a way how to amend polymer composition during regranulation to create raw material for spunmelt production. I personally see a big potential in this field; our findings might be applicable in the future, especially with respect to polymer mixtures from various sources. Last but not least, I personally appreciate the approach PFN is taking in the field and their focus on sustainability."
Simon Frisk, Global Head of RD at PFN adds: “This project is another great example of the power of collaboration between industry and academia, and between PFN and UTB in particular. Together, we study and develop solutions to complex fundamental polymer issues or developments. The deep polymer knowledge and expertise of UTB, together with their advanced laboratory capabilities, constitute an ideal partner for PFN to tackle some of our more complex challenges. The solutions developed in the laboratories are then rapidly applied to our commercial operations, providing students with direct examples of how laboratory work can have a big impact in the industry. For this particular project, the impact goes beyond good science and technology development. It will enable the reduction of the environmental footprint of our products by reducing waste and reusing raw materials, contributing to PFN’s overall drive to be an industry leader in sustainability.”
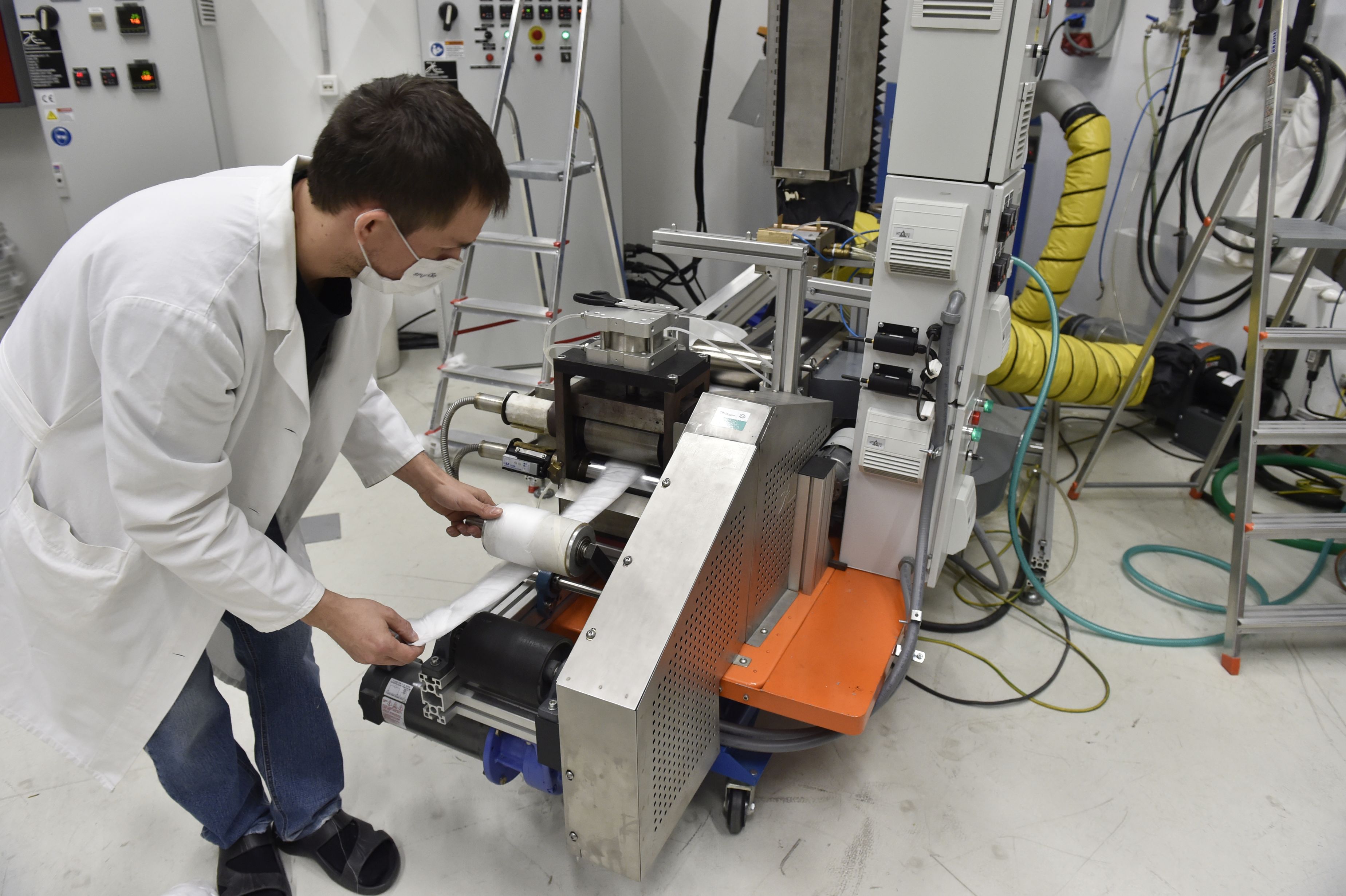
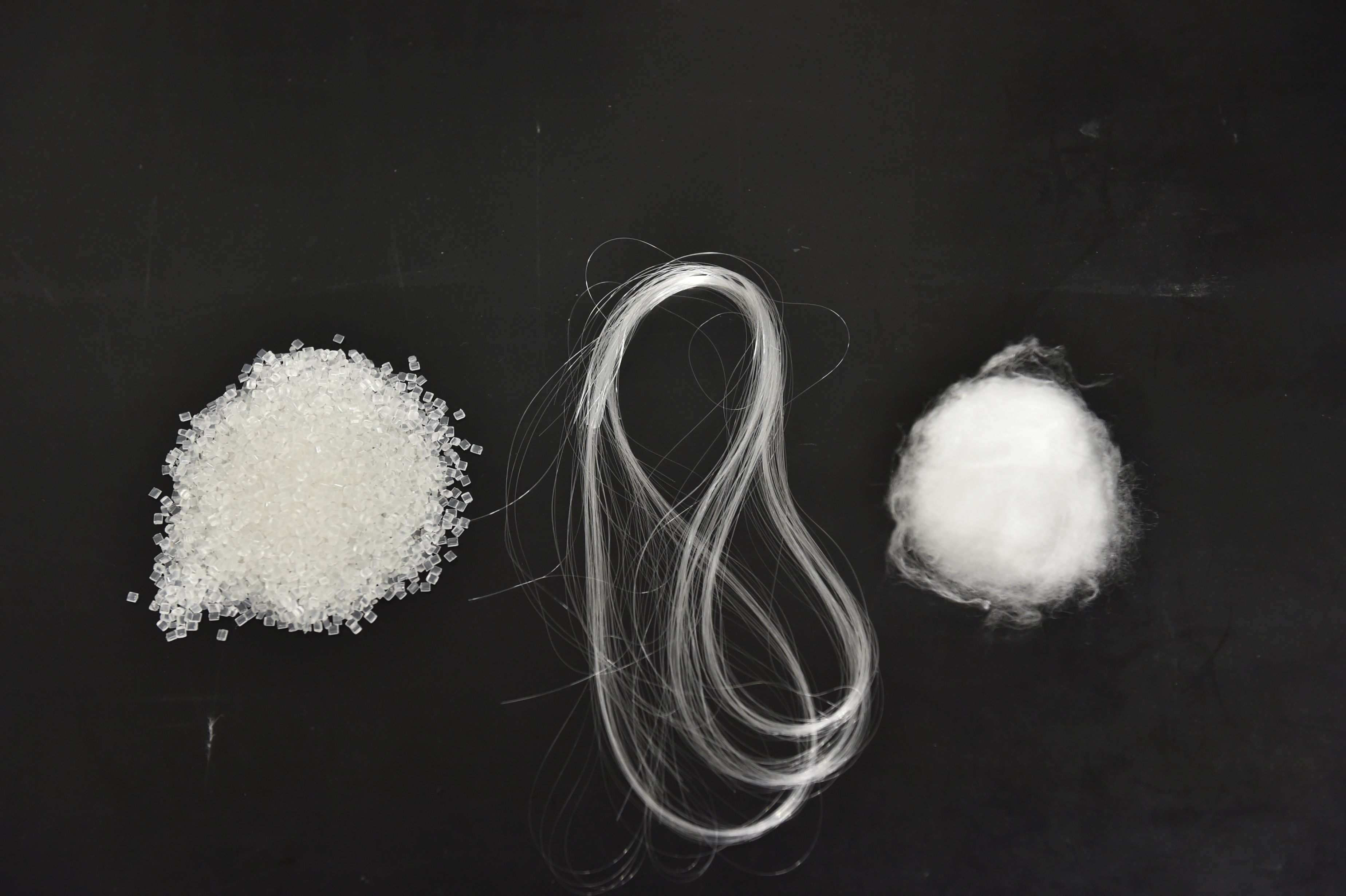
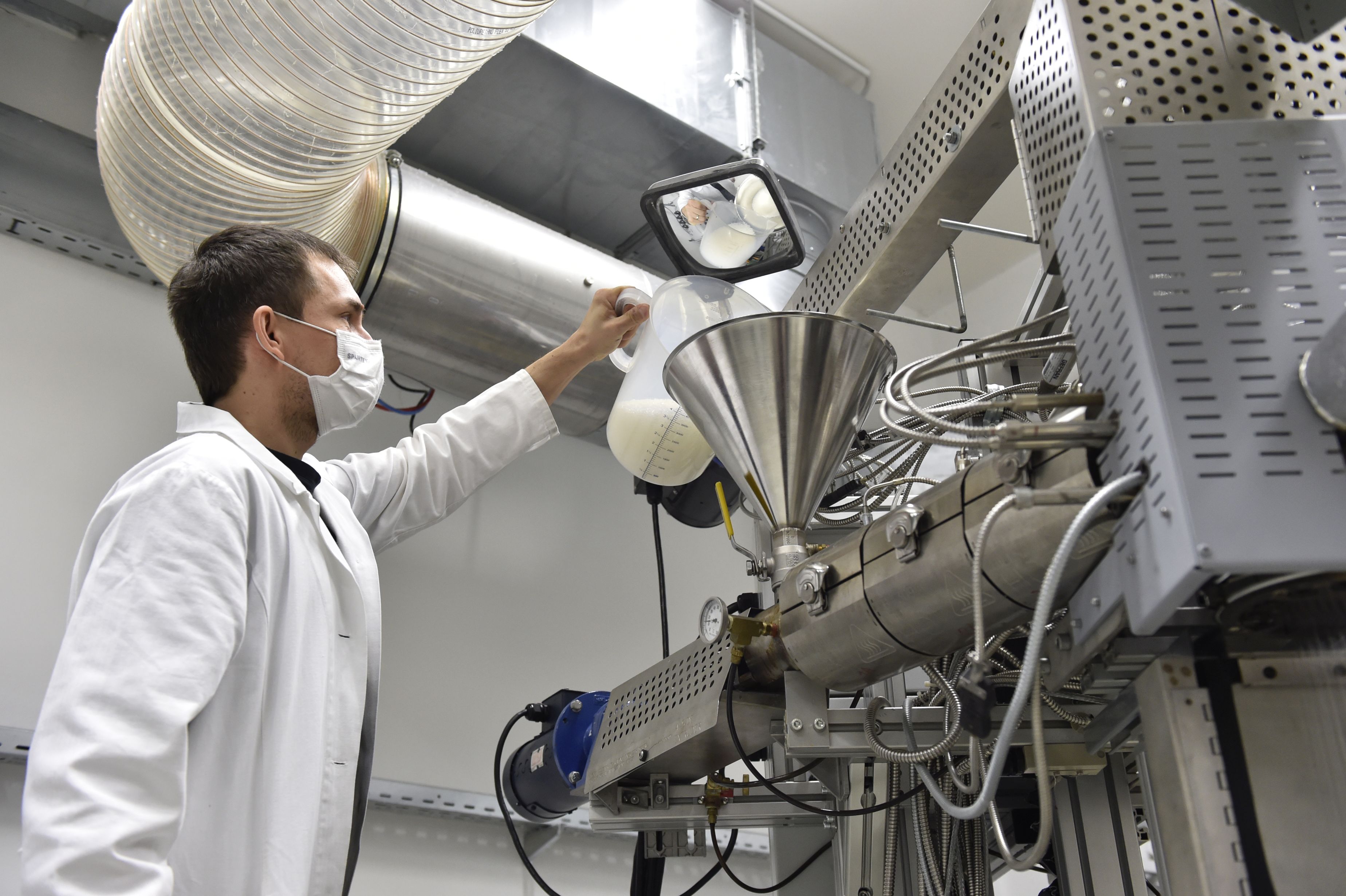